
PRYSM Inc.
Summer 2016
PRYSM is a company that develops Laser Phosphor Display (LPD) video wall technology, as well as collaboration software that can be used on the video walls and other devices. Within each tile of a video wall is an optical scanning system involving a rotating polygon that directs laser beams at phosphor stripes that activate and produce an image.
At PRYSM, I was tasked with automating the procedure for profiling the laser beams at user specified locations on the phosphor panel. The process of moving the beam profiler to the desired location on the screen plane was already automatic. To profile the beam, the operator would rotate the polygon until the beam was at the desired location, and then take data from the profiler. The operator could not touch the mirrors of the polygon, and could not press with too much pressure because the polygon was resting in an air bearing. My goal was to automate polygon rotation to eliminate operator’s requirement to position polygon for the different screen plane test locations. This will also allow for long duration, fully automated testing anywhere on the screen. This new test method saved the engineers hours every day, thus saving the company thousands of dollars in the testing of each light engine.
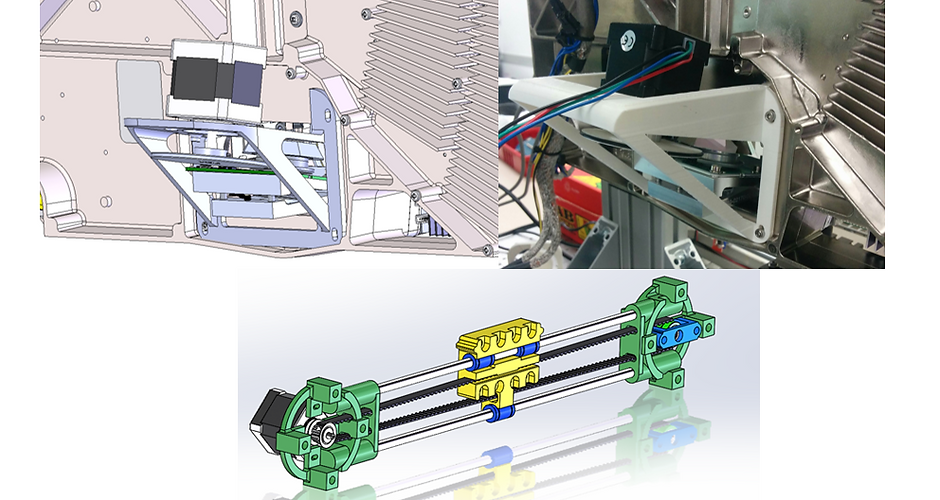
How It Works
-
Motorized belt moves sheet of diffuser material in front of laser to allow camera to locate beam
-
Stepper motor, controlled by Arduino, rotates mirrored polygon
-
Thorlab’s Camera tracks beam on scan lens
-
Software maps beam location to the screen plane
-
Predicts panel spot location using laser spot on diffuser to +/-2 mm
-
Arduino receives new position and moves stepper motor
-
Polygon rotator easily attaches to LE
-
3D printed components in-house with ABS
-
All components controlled with LabVIEW and Arduino

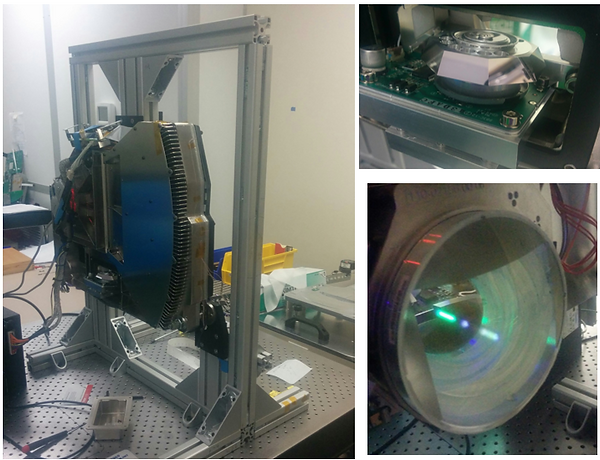

